STEEL
High Temp Fans for the Steel Industry
High temperature fans play a critical role in the midstream and downstream steel production processes to ensure workability and optimal final material properties.
The right, high quality air-moving equipment ensures process stability (including oxidation reduction and atmosphere control), energy efficiency, and operational reliability to maintain product quality and minimize cost. Inferior quality or incorrect fan selection can lead to inefficient operations at best and extensive lost production from unplanned downtime & excessive quality waste at worst. The role of fans is even more important where electric heating sources are being considered.
IGE’s production-proven designs with innovative shaft sealing methods are particularly critical in tempering, annealing, normalizing, and hardening applications across plate, sheet, strip, coil, wire, rebar, rod, pipe & tube, and forgings.
Leaders in the global steel industry trust IGE FANS to deliver the right, high-quality equipment for many applications:
Steel temper furnaces
Tempering places a critical role in the production of hardened steels by reducing brittleness and internal strains caused by the quench process. The process involves heating the metal to a specific temperature, holding it there for a specific period of time, then cooling at a controlled rate. Higher temperatures will result in higher ductility but lower strength and hardness values. Lower temperatures maintain higher strength and hardness, but at the cost of low ductility.
Given high temperatures, typically 600-1400°F (300-750°C), and the need to maintain tight temperature control, uniformity, and cooling rates, high-quality, well-engineered high temperature fans are critical.
IGE offers a range of axial, forward curved, radial, and backward inclined fan designs that are suitable for tempering processes of various scales and configurations. IGE offers innovative shaft sealing methods that ensure process stability, energy efficiency, and improved safety and offers both air-cooled and water-cooled designs.
Steel annealing furnaces
Annealing furnaces soften steel, improve ductility, and refine grain structure by heating the steel to a specific temperature, holding it there for a specific period of time, then cooling at a controlled rate. Annealing is often completed in preparation for further machining or forming. Coil annealing is a very common application and there are many permutations of equipment based on size and batch vs. continuous.
Significant airflow is required to ensure temperature uniformity and effective convective heat transfer to minimize cycle times. Forward curved centrifugal and axial fans are often used in these applications. IGE has a wide range of production-proven designs that can serve any size or configuration – batch or continuous.
Steel stress relieving furnaces
Stress relieving furnaces are used to relieve internal stresses caused by working or forming without reaching critical transformation temperatures that significantly impact the hardness & ductility of the steel.
IGE offers a range of axial, forward curved, radial, and backward inclined fan designs that are suitable for stress relieving processes of various scales and configurations. IGE offers innovative shaft sealing methods that ensure process stability, energy efficiency, and improved safety and offers both air-cooled and water-cooled designs.
Steel heat treating furnaces
In the primary steel industry, heat treatment of forgings is one of the most common heat-treating processes that yields final parts for sale. Forgings are commonly reheated, quenched, and tempered to attain the ideal final material characteristics for products like wheels and roll rings.
IGE has air moving equipment suitable for heat treat furnaces of all sizes and configurations. Typically thought of as processes in secondary metals (vs. primary), IGE also has solutions for a vast set of steel heat treating processes including carburizing, nitriding, carbonitriding, and more.
Steel reheat furnaces
Reheat furnaces are used to prepare steel billets, blooms, slabs, and ingots for subsequent forming steps including long product (e.g., wire rod, bar, etc.) hot rolling, pipe hot rolling, and forging.
IGE’s fans are often used in these applications. IGE has a wide range of production-proven designs that can serve any size or configuration – batch or continuous.
Steel sintering furnaces
Sintering furnaces compact and bond powdered metal particles at high temperatures in highly controlled environments. Strict temperature and atmosphere control are essential to prevent oxidation and ensure high-quality output.
IGE has experience across a wide range of sintering applications and has innovative shaft sealing methods that ensure process stability, energy efficiency, and improved safety and offers both air-cooled and water-cooled designs. IGE also offers direct-drive sealed motors that offer vacuum-level seal quality as well as innovative, positive-pressure-atmosphere seal enclosures to maximize atmosphere & process control.
Carbon baking furnaces
Carbon baking is a critical step in electrode and fine-grained carbon production. Car bottom furnaces are the most common structure in this application and typically use axial fans to maximize convection heating and minimize cycle time with operating temperatures near 1500°F.
Related Products
Related Applications
IGE Fans Advantage
Industry-leading Reliability, Support & 2-Year Warranty
6 Week Lead Time & Expedited Service
US Based Supply Chain
Unmatched Dynamic Balance Capabilities
100+ Years of Deep Process Expertise
Elevate your operations with high-performance industrial fans from IGE
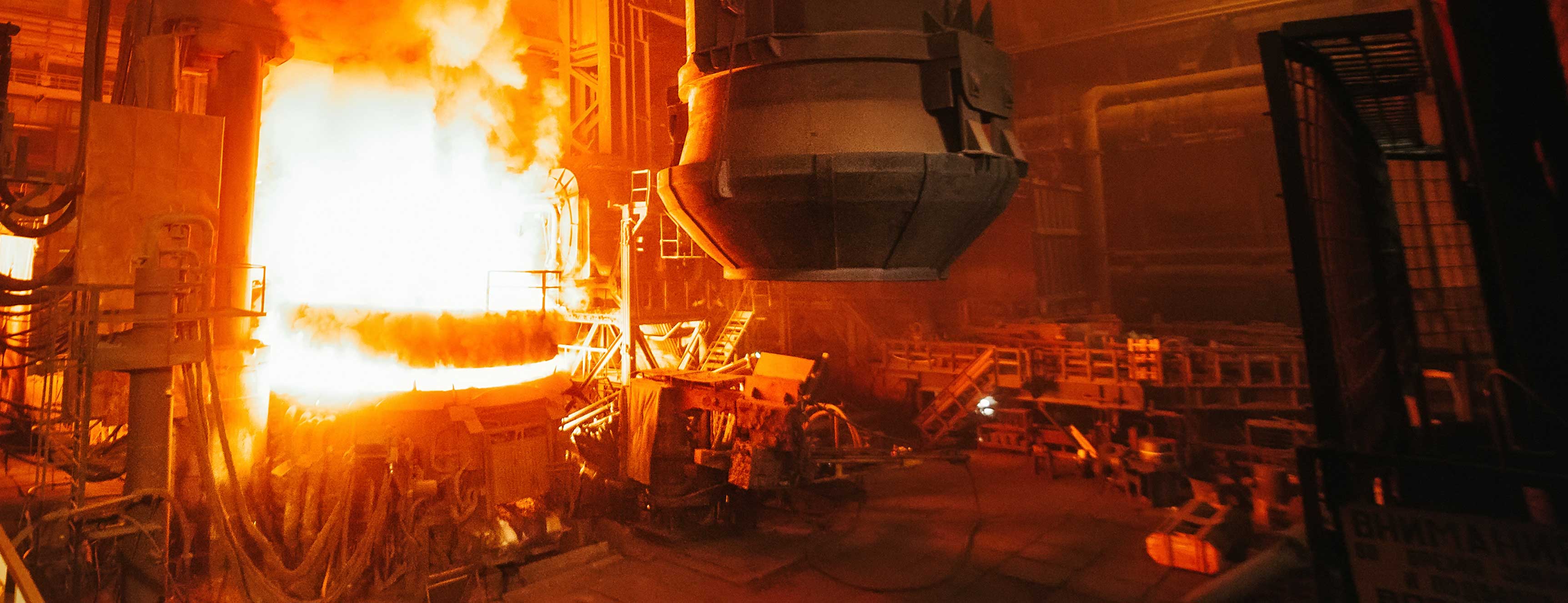
Ready for a fan partner that does more than blow hot air?
IGE Fans will extend the service life of your equipment, improve process control, and reduce costs.